Heat Treatment Department
Any Wear part can have an excellent wear resistance property only if the Heat treatment process carried out on it is proper. Any short cut in this process will lead to a poorer microstructure resulting in low hardness and low Abrasive wear resistance properties.
TARC has a full fledge in house Heat treatment shop with 2 Electric furnaces with fan attachment giving uniform heating to the castings. In-house Quenching facilities like OIL, WATER & AIR is available with us.
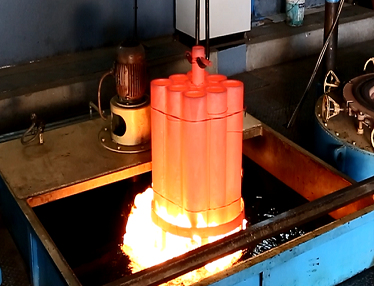
Oil quenching is a common method for hardening alloy steel forgings. It is ideal for achieving the required strength and hardness properties on many alloys.
Oil Quenching
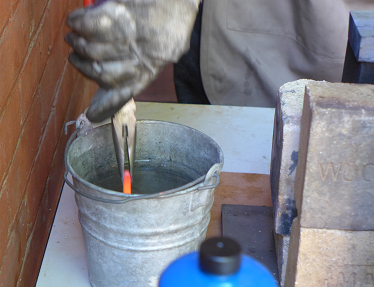
When hardness can be sacrificed, mineral oils are often used. These oil-based fluids often oxidize and form a sludge during quenching, which consequently lowers the efficiency of the process.
Water Quenching
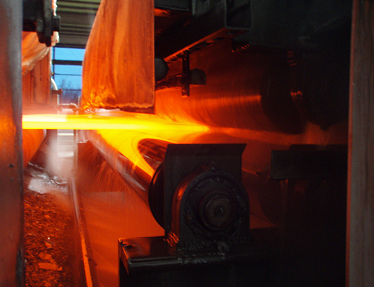
Air quenching is used as a means to limit the residual stresses as well as the brittleness that occurs during the quenching process. Rapid quenching also has a tendency.
Air Quenching Process
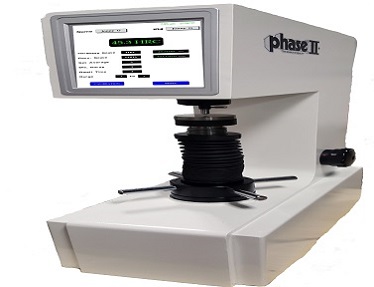
There are many hardness tests currently in use. The neccessity for all these different hardness tests is due to the need for categorizing the great range of hardness from soft rubber to hard ceramics.
Hardness testing facilities Ni Hard Micro Structure

Ni-Hard is the generic name for a Family of white cast irons alloyed with nickel and chromium to give high hardness and outstanding resistance to abrasion.
Ni-Hard Micro Structure After Heat Treatment
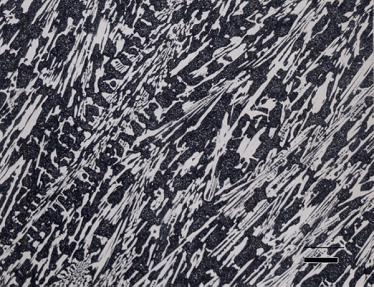
In this form the material is suitable for service in wear resisting application due to the inherent capabilities of austenite to transform to martensite and to increase its hardness in the working environment.